Единая система защиты от коррозии и старения. Стали и сплавы высокопрочные. Методы ускоренных испытаний на коррозионное растрескивание
ГОСТ 9.903-81
Группа Т99
Дата введения 1982-07-01
ВВЕДЕН В ДЕЙСТВИЕ постановлением Государственного комитета СССР по стандартам от 2 апреля 1981 г. N 1765
Настоящий стандарт распространяется на высокопрочные стали и титановые сплавы (далее - материалы) и устанавливает методы ускоренных испытаний на коррозионное растрескивание образцов с предварительно созданными усталостными трещинами.
Сущность методов заключается в том, что образцы подвергают одновременному воздействию коррозионной среды и растягивающих напряжений, при котором поверхности трещины расходятся в направлении действующих напряжений симметрично относительно плоскости исходной трещины.
Стандарт устанавливает три метода испытаний:
1 - при постоянной нагрузке;
2 - при ступенчато изменяемой нагрузке;
3 - при постоянной деформации.
Критерием оценки стойкости материала к коррозионному растрескиванию является пороговый коэффициент интенсивности напряжений .
Значения определяют для заданной продолжительности испытаний и (или) для условно принятого значения скорости роста трещины.
Значения не могут быть использованы для оценки влияния на стойкость к коррозионному растрескиванию факторов, изменяющих поверхностные свойства материалов (защитных покрытий, поверхностного упрочнения и т. п.).
Термины, применяемые в стандарте, и их определения приведены в приложении 1.
1. МЕТОД 1
1.1. Сущность метода определения при постоянной нагрузке на образец состоит в испытании серии образцов при различных исходных значениях коэффициента интенсивности напряжений при плоской деформации и продолжительности испытаний 40 сут.
Допускается определять при другой продолжительности испытаний, установленной в технических условиях на материал, при этом сравнительные испытания материалов проводят при продолжительности испытаний 40 сут.
1.2. Требования к образцам
1.2.1. Минимальную толщину образцов ( ) в миллиметрах ориентировочно вычисляют по формуле
,
где - коэффициент интенсивности напряжений при плоской деформации, МПа·м , в интервале от до ;
- условный предел текучести материала при растяжении, МПа;
- определяют по нормативно-технической документации.
Для новых материалов ориентировочное значение выбирают по приложению 2 для материалов, близких по химическому составу, механическим и коррозионным свойствам.
Основными критериями выбора толщины образцов являются образование в процессе роста трещин поверхностей разрушения, перпендикулярных направлению действия растягивающих напряжений, и отсутствие макроскопического разветвления растущих трещин, т.е. рост в процессе испытаний одной магистральной трещины. Эти критерии могут быть определены только после проведения предварительных испытаний. Если эти условия не выполняются, испытания повторяют на образцах толщиной 2 .
Если толщина , определенная по формуле, составляет доли миллиметра, определение проводят на образцах сталей толщиной не менее 1 мм и титановых сплавов не менее 5
мм.
1.2.2. Применяют следующие типы образцов в зависимости от приложения нагрузки:
ОР - осевое растяжение;
КИ - консольный изгиб;
ВРI и ВРII - внецентровое растяжение.
Тип, форма и размеры образцов приведены в приложении 3.
1.2.3. Вырезку образцов из полуфабрикатов проводят в соответствии с приложением 4.
Направление вырезки образца обозначают двумя буквами, первая из которых указывает направление нормали к плоскости трещины, а вторая - направление развития трещины в этой плоскости, и вносят в протокол испытаний рекомендуемого приложения 5.
1.2.4. Проводят замер образцов. Длину, ширину и толщину образцов вычисляют как среднее арифметическое трех измерений. Данные измерений вносят в протокол испытаний.
1.2.5. Количество образцов должно быть не менее трех при каждом значении начальной нагрузки, для данного состояния материала и направления вырезки образца.
1.2.6. Образцы подвергают термической обработке в соответствии с требованиями стандартов или технических условий на материал.
1.3. Аппаратура, материалы и реактивы
1.3.1. Машины или приспособления, предназначенные для испытаний металлов и сплавов на ползучесть и длительную прочность в соответствии с требованиями ГОСТ 3248-81 и ГОСТ 10145-80*. __________________ * Вероятно ошибка оригинала. Следует читать ГОСТ 10145-81. Примечание.
1.3.2. Машины или вибраторы, обеспечивающие циклическое нагружение образцов при симметричном или пульсирующем цикле нагружения, типа универсальной испытательной машины МУП-20 по ГОСТ 28840-90.
1.3.3. Микроскопы или другие приборы, позволяющие определять длину трещины с погрешностью не более 0,05 мм.
1.3.4. Коррозионная среда - 3%-ный раствор хлористого натрия по ГОСТ 4233-77 в дистиллированной воде по ГОСТ 6709-72. В зависимости от условий эксплуатации реальных изделий допускается применять другие коррозионные среды.
1.3.5. Спирт этиловый по ГОСТ 5962-67.
1.3.6. Эксикатор по ГОСТ 25336-82.
1.4. Подготовка к испытаниям
1.4.1. Образцы обезжиривают и промывают этиловым спиртом.
1.4.2. Усталоcтную трещину получают на воздухе при циклическом растяжении или изгибе на машинах (п.1.3.2) на полностью термически обработанных образцах. Циклическое нагружение подбирают таким образом, чтобы скорость роста усталостной трещины на последнем миллиметре не превышала 1 мм за 50000 циклов.
Не допускается применять окрашивающие растворы для облегчения контроля за ростом усталостной трещины.
1.4.3. Измеряют расчетную длину исходной трещины (механический надрез + усталостная трещина).
Длина усталостной трещины должна быть не менее 1,5 мм, не менее 5% длины исходной трещины и не менее толщины образца.
Разность длин усталостной трещины на обеих сторонах образца не должна превышать 10%. Если это требование не выполняется, необходимо продолжить циклическое нагружение, предварительно повернув образец на 180° (оснастка при этом остается в первоначальном положении).
Результаты измерений вносят в протокол испытаний.
1.4.4. Отклонение усталостной трещины от плоскости симметрии надреза не должно превышать 10°.
1.4.5. Образцы маркируют по ГОСТ 9.019-74. Маркировку наносят на расстоянии не менее 20 мм от плоскости исходной усталостной трещины. Данные вносят в протокол испытаний.
1.4.6. Подготовленные к испытаниям образцы с усталостной трещиной хранят в эксикаторе.
1.4.7. Определяют критический коэффициент интенсивности напряжений на воздухе .
1.5. Проведение испытаний
1.5.1. Образцы устанавливают в захваты испытательной машины и подводят коррозионную среду. Объем раствора на 1 см поверхности образца должен быть не менее 10 см .
1.5.2. Образцы нагружают до значения начального коэффициента интенсивности напряжений , который вычисляют по формуле
,
где .
Расчетные значения вносят в протокол испытаний.
1.5.3. Испытания проводят при температуре 291-298 К (18-25 °С). Допускается проводить испытания при температурах, соответствующих условиям эксплуатации изделий.
1.5.4. Проводят контроль за разрушением образцов через 0,5 ч после начала испытаний, далее через 1, 2, 4, 6, 8 ч, далее четыре раза в сутки. Допускаются другие интервалы времени.
1.5.5. Фиксируют время до разрушения образцов и вносят его в протокол испытаний.
1.5.6. Если за 40 сут образцы не разрушились, их разгружают, снимают с испытательной машины, высушивают при температуре 373-423 К (100-150 °С) и разрушают на испытательной машине на воздухе.
1.5.7. Определяют конечную длину трещины (исходная трещина + коррозионная трещина) всех образцов как среднее арифметическое трех измерений: на 1/4, 1/2, и 3/4 толщины. Результаты измерений вносят в протокол испытаний.
1.5.8. По конечной длине трещины и формулам (п.1.6.4) вычисляют действительное значение . Данные вносят в протокол испытаний.
1.5.9. Образцы с коррозионной трещиной более 0,1 мм относят к разрушившимся образцам.
1.5.10. Если за 40 сут разрушились все образцы при , определение повторяют в интервале от =0 до =0,1 .
1.5.11. Если ни один из образцов не разрушился (в том числе при ), определяют по методу 2.
1.5.12. Определение проводят с погрешностью не более 10%.
1.6. Обработка результатов
1.6.1. определяют графическим или расчетным способом.
1.6.2. Графический способ определения состоит в построении зависимости , где - время до разрушения образцов.
За принимают коэффициент интенсивности напряжений, соответствующий времени испытаний 40 сут.
1.6.3. По расчетному способу вычисляют как среднее арифметическое трех минимальных значений разрушившихся и трех максимальных значений неразрушившихся образцов.
Если разность значений более 10%, определяют в более узком интервале ( ).
1.6.4. , и вычисляют по формулам:
для образцов типа ОР
,
где - нагрузка на образец, Н;
- конечная длина трещины, м;
- толщина образца, м;
- ширина образца, м;
- коэффициент, вычисляемый по формуле
;
для образцов типа КИ
,
где - изгибающий момент, Н·м;
- коэффициент, вычисляемый по формуле
, где ;
для образцов типа ВР
,
где - коэффициент, рассчитываемый по формулам:
для ;

для , где - размер образца, определяемый по черт.3 приложения 3, м.
Значения , и приведены в приложении 6.
1.6.5. Значения вносят в протокол испытаний.
2. МЕТОД 2
2.1. Сущность метода определения при ступенчато изменяемой нагрузке на образец (метод остановки трещины вне зоны пластической деформации у вершины исходной усталостной трещины) состоит в постепенном ступенчатом увеличении нагрузки на образец до начала роста трещины, проращивании трещины через исходную зону пластической деформации не менее 1 мм для высокопрочных сталей и 2,5 мм для титановых сплавов и постепенном снижении нагрузки до полной остановки роста трещины.
За принимают коэффициент интенсивности напряжений, соответствующий остановке трещины.
2.2. Требования к образцам - по п.1.2.
Количество образцов не менее трех для данного состояния материала и направления вырезки образца.
2.3. Аппаратура, материалы и реактивы
2.3.1. Машины или приспособления, предназначенные для статического нагружения и обеспечивающие возможность проведения следующих операций:
измерять и поддерживать постоянную нагрузку в течение всего процесса испытаний с погрешностью не более 1%;
плавно нагружать образцы;
надежно центрировать образцы (например, машина разрывная типа Р-5 по ГОСТ 28840-90).
2.3.2. Машины или вибраторы - в соответствии с требованиями п.1.3.2.
2.3.3. Микроскопы или другие приборы - в соответствии с требованиями п.1.3.3.
2.3.4. Установки, обеспечивающие непрерывное измерение длины трещины и непрерывную запись измеряемого параметра, чувствительностью не ниже 0,001 мм прироста трещины.
Схема установки для непрерывного контроля за ростом трещины приведена в рекомендуемом приложении 7.
2.3.5. Схемы потенциометрические и мостовые на постоянном и переменном токе, обеспечивающие измерение электрического сопротивления центральной части образца.
2.3.6. Датчики перемещения тензометрические, трансформаторные и индукционные, обеспечивающие измерение раскрытия трещины, не влияющие на коррозионный процесс.
2.3.7. Коррозионная среда для проведения испытаний - по п.1.3.4.
2.4. Подготовка к испытаниям
2.4.1. Подготовка к испытаниям проводится по пп.1.4.1-1.4.7.
2.4.2. Для любого из методов измерения приращения трещины делают градуировку, определяющую в абсолютных или относительных единицах приращение трещины в зависимости от изменения измеряемого параметра (электрического сопротивления, раскрытия трещины и т. п.).
Градуировку проводят на образцах из серии подготовленных к испытаниям путем замера конечной длины трещины (п.1.5.7) с одновременным измерением калибруемого параметра (п.2.3.4).
2.5. Проведение испытаний
2.5.1. Испытания проводят при температуре, указанной в п.1.5.3.
2.5.2. Образцы устанавливают в захваты испытательной машины, подводят коррозионную среду, нагружают образцы, повышая нагрузку до начала роста трещины, проращивают трещину (п.2.1) и затем снижают нагрузку.
Повышают и снижают нагрузку произвольно, но после снижения скорости роста трещины до 10 -10 мм/ч необходимо снижать нагрузку на 2-3%. После остановки трещины убеждаются в отсутствии ее роста в течение 10 ч, при этом приращение трещины должно быть менее 0,001 мм, и фиксируют нагрузку остановки трещины.
Нагрузку снижают до нуля, снимают образцы с испытаний, высушивают при температуре 373-423 К (100-150 °С) и разрушают на воздухе на испытательной машине.
2.5.3. Определяют конечную длину трещины (п.1.5.7). Конечная длина трещины должна быть не более 70% ширины образца.
2.6. Обработка результатов
2.6.1. По нагрузке остановки трещины, конечной длине трещины, определенных по пп.2.5.2; 2.5.3 и 1.6.4, вычисляют . Данные вносят в протокол испытаний.
2.6.2. можно определить методом экстраполяции. Для этого строят зависимость логарифма скорости роста трещины от коэффициента интенсивности напряжения. Экстраполируют участок кривой (в интервале 0,1-0,001 мм/ч) до скорости роста трещины 0,0001 мм/ч. За принимают коэффициент интенсивности напряжений, соответствующий этой скорости роста трещины.
3. МЕТОД 3
3.1. Метод определения при постоянной деформации применяют только на образцах типа ВР. Метод состоит в задании фиксированной деформации, выдержке образцов в коррозионной среде и контроле роста трещины. В процессе роста трещины податливость образца увеличивается и значение коэффициента интенсивности напряжения уменьшается, вследствие чего скорость роста трещины снижается до полного прекращения роста.
За принимают коэффициент интенсивности напряжений, соответствующий прекращению роста трещины или снижению скорости роста трещины до 0,0001 мм/ч за 40 сут.
3.2. Требования к образцам - по п.1.2.
Количество образцов должно быть не менее трех на каждое значение деформации для данного состояния материала и направления вырезки образца.
3.3. Аппаратура, материалы и реактивы
3.3.1. Машины и приспособления, жесткость которых не менее, чем в 10 раз больше жесткости образца в начале испытаний, позволяющих осуществить плавное нагружение образцов, надежное их центрирование и обеспечивать постоянную заданную деформацию образца в процессе испытаний, например, приспособление для нагружения образца типа ВР1 (рекомендуемое приложение 8). Образец типа ВР11 нагружают с помощью винта и центрирующего вкладыша.
3.3.2. Машины или вибраторы - в соответствии с требованиями п.1.3.2.
3.3.3. Микроскопы или другие приборы - в соответствии с требованиями п.1.3.3.
3.3.4. Коррозионная среда для проведения испытаний - по п.1.3.4.
3.4. Подготовка к испытаниям - по п.1.4.
3.4.1. При определении записывают диаграмму, "нагрузка - раскрытие трещины". Получают зависимость нагрузки от деформации для образцов данной конфигурации. Эту зависимость используют для расчета исходной деформации образца, необходимой для получения выбранного значения .
3.5. Проведение испытаний
3.5.1. Нагружение образцов проводят до .
3.5.2. Образцы с приспособлением помещают в коррозионную среду и контролируют рост трещины (п.2.3.4). Если после начала испытаний трещина не растет в течение 15 сут, повышают на 20%. После начала роста трещины дальнейшее повышение не допускается. Испытания проводят до полной остановки трещины.
3.6. Обработка результатов
3.6.1. Определяют нагрузку остановки трещины . Для этого образец разгружают, регистрируют величину сближения поверхностей трещины, производят повторное деформирование на испытательной машине на воздухе на эту величину и определяют .
3.6.2. Определяют конечную длину трещины (п.1.5.7) и вычисляют по нагрузке остановки трещины и формулам п.1.6.4.
Результаты вносят в протокол испытаний.
ПРИЛОЖЕНИЕ 1 (справочное). ТЕРМИНЫ И ОПРЕДЕЛЕНИЯПРИЛОЖЕНИЕ 1 Справочное
Термин
| Определение | Коэффициент интенсивности напряжений ( )
| Величина, характеризующая интенсивность напряжений вблизи вершины трещины в линейно-упругой среде при отрывном типе деформации (поверхности трещины отходят друг от друга по нормали) в условиях трехосного напряженного состояния материала (при плоской деформации)
| Критический коэффициент интенсивности напряжений на воздухе ( )
| Коэффициент интенсивности напряжений при плоской деформации, соответствующий разрушающей нагрузке при статических испытаниях на воздухе
| Начальный коэффициент интенсивности напряжений при испытаниях на коррозионное растрескивание ( )
| Коэффициент интенсивности напряжений при испытаниях на коррозионное растрескивание, определяемый по значениям начальной нагрузки на образец и начальной длины концентратора напряжений (механический надрез+усталостная трещина)
| Пороговый коэффициент интенсивности напряжений при коррозионном растрескивании ( )
| Коэффициент интенсивности напряжений при плоской деформации, характеризующий сопротивление материала росту трещины при коррозионном растрескивании (в данных условиях: электролит, температура и т. п.), ниже которого рост трещины отсутствует или скорость роста не превышает 0,0001 мм/ч
|
ПРИЛОЖЕНИЕ 2 (справочное). ОРИЕНТИРОВОЧНЫЕ ЗНАЧЕНИЯ КIKP В 3%-ном РАСТВОРЕ ХЛОРИСТОГО НАТРИЯ ПРИЛОЖЕНИЕ 2 Справочное
Марка
| , МПа·м
| Высокопрочные стали*
| 30ХГСНА
| 17
| 28Х3СНМВФА
| 16
| 42Х2ГСНМА
| 12
| 03Н18Х9М5Т
| 10
| 000Х12К13Н5М5Т
| 50
| Титановые сплавы**
| ВТ-20
| 46
| ВТ6
| 56
| ВТ5-1
| 40
| ВТ-15
| 35
| ___________ * После термической обработки на максимальную прочность.
** Горячекатаный лист.
|
ПРИЛОЖЕНИЕ 3 (обязательное). ТИПЫ ОБРАЗЦОВ ПРИЛОЖЕНИЕ 3 Обязательное
Черт.1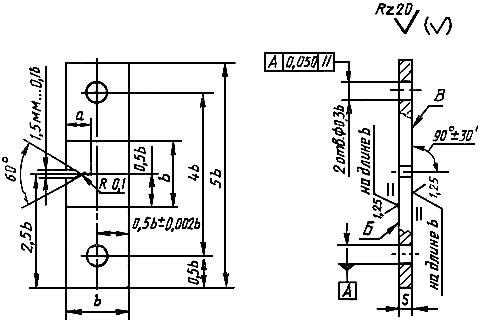
Черт.1
Примечания:
1. Непараллельность плоскостей , не более 0,01 на длине 10 мм.
2. .
3. , где - длина исходной трещины (механический надрез + усталостная трещина), мм. Черт.2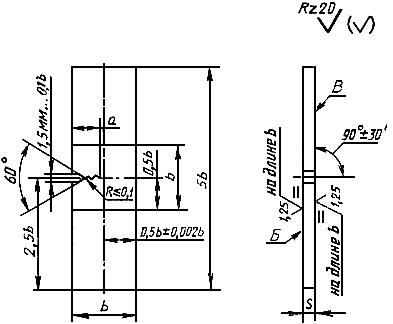
Черт.2
Примечания:
1. мм.
2. Непараллельность плоскостей , не более 0,01 на длине 10 мм.
3. .
4. , где - длина исходной трещины (механический надрез + усталостная трещина), мм.
Черт.3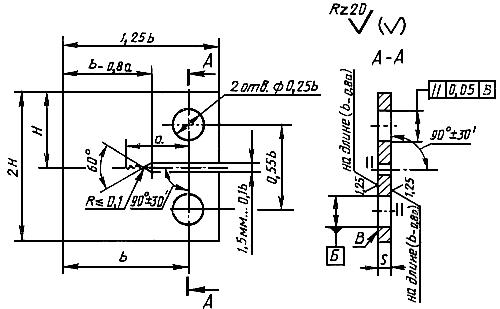
Черт.3
Примечания:
1. мм.
2. Непараллельность плоскостей , не более 0,01 на длине 10 мм.
3. .
4. , где - длина исходной трещины (механический надрез+усталостняя трещина), мм.
5. или .
Черт.4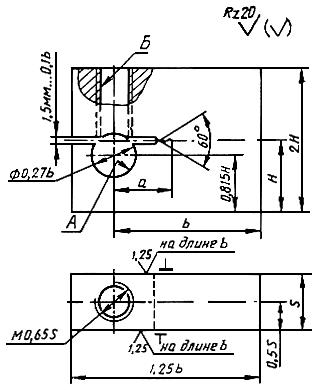
Черт.4
Примечания:
1. Неперпендикулярность оси отверстия относительно оси отверстия не более .
2. .
3. , где - длина исходной трещины (механический надрез+усталостная трещина), мм
4. .
ПРИЛОЖЕНИЕ 4 (обязательное). СХЕМА ВЫРЕЗКИ ОБРАЗЦОВПРИЛОЖЕНИЕ 4 Обязательное Листы, штамповки, поковки прямоугольного сечения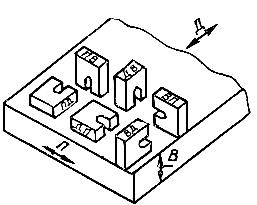
_______________ * Направление вырезки только и .
Полуфабрикаты цилиндрического вида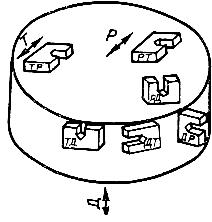
Направление вырезки: - долевое, вдоль главного вектора деформации; В - высотное; - поперечное; - радиальное; - тангенциальное
ПРИЛОЖЕНИЕ 5 (рекомендуемое). ПРОТОКОЛ ИСПЫТАНИЙПРИЛОЖЕНИЕ 5 Рекомендуемое
Марки- ровка образца
| Механи- ческие свойства
| Тип образца
| Длина трещины, мм
| Корро- зионная среда
| Темпе- ратура среды, К
| Метод опре- деления | , МПа·м
| , МПа·м
| | , МПа
| , МПа
| Обозна- чение
| Направ- ление вырезки
| Тол- щина
| Ши- рина
| Длина
| исход- ная
| конеч- ная
| | | | расчет- ный
| дей- стви- тель- ный
| |
|
|
|
|
|
|
|
|
|
|
|
|
|
|
|
|
ПРИЛОЖЕНИЕ 6 (справочное) ПРИЛОЖЕНИЕ 6 Справочное
|
|
|
|
| 0,20
| 2,43
| 1,20
| 5,19
| 5,70
| 0,21
| 2,48
| 1,24
| 5,22
| 5,75
| 0,22
| 2,52
| 1,28
| 5,25
| 5,81
| 0,23
| 2,57
| 1,32
| 5,29
| 5,88
| 0,24
| 2,62
| 1,36
| 5,34
| 5,95
| 0,25
| 2,67
| 1,40
| 5,41
| 6,04
| 0,26
| 2,72
| 1,44
| 5,48
| 6,14
| 0,27
| 2,77
| 1,48
| 5,56
| 6,24
| 0,28
| 2,83
| 1,52
| 5,65
| 6,36
| 0,29
| 2,89
| 1,56
| 5,74
| 6,48
| 0,30
| 2,95
| 1,60
| 5,85
| 6,60
| 0,31
| 3,01
| 1,65
| 5,96
| 6,74
| 0,32
| 3,08
| 1,69
| 6,09
| 6,88
| 0,33
| 3,15
| 1,74
| 6,22
| 7,02
| 0,34
| 3,22
| 1,79
| 6,35
| 7,17
| 0,35
| 3,30
| 1,83
| 6,50
| 7,33
| 0,36
| 3,38
| 1,88
| 6,65
| 7,49
| 0,37
| 3,46
| 1,94
| 6,81
| 7,66
| 0,38
| 3,55
| 1,99
| 6,97
| 7,83
| 0,39
| 3,64
| 2,04
| 7,14
| 8,00
| 0,40
| 3,73
| 2,10
| 7,32
| 8,18
| 0,41
| 3,83
| 2,16
| 7,51
| 8,36
| 0,42
| 3,94
| 2,22
| 7,70
| 8,55
| 0,43
| 4,05
| 2,28
| 7,91
| 8,74
| 0,44
| 4,17
| 2,35
| 8,12
| 8,94
| 0,45
| 4,29
| 2,42
| 8,34
| 9,15
| 0,46
| 4,42
| 2,49
| 8,37
| 9,36
| 0,47
| 4,56
| 2,56
| 8,81
| 9,58
| 0,48
| 4,70
| 2,64
| 9,06
| 9,82
| 0,49
| 4,86
| 2,72
| 9,32
| 10,06
| 0,50
| 5,02
| 2,81
| 9,60
| 10,31
| 0,51
| 5,18
| 2,90
| 9,90
| 10,58
| 0,52
| 5,36
| 2,99
| 10,21
| 10,87
| 0,53
| 5,55
| 3,09
| 10,54
| 11,17
| 0,54
| 5,74
| 3,19
| 10,89
| 11,49
| 0,55
| 5,95
| 3,30
| 11,26
| 11,83
| 0,56
| 6,16
| 3,41
| 11,66
| 12,20
| 0,57
| 6,39
| 3,54
| 12,08
| 12,60
| 0,58
| 6,63
| 3,66
| 12,54
| 13,03
| 0,59
| 6,88
| 3,80
| 13,02
| 13,49
| 0,60
| 7,14
| 3,94
| 13,54
| 13,98
| 0,61
| 7,42
| 4,10
| 14,10
| 14,52
| 0,62
| 7,71
| 4,26
| 14,70
| 15,10
| 0,63
| 8,01
| 4,44
| 15,34
| 15,73
| 0,64
| 8,33
| 4,62
| 16,04
| 16,42
| 0,65
| 8,67
| 4,83
| 16,78
| 17,16
| 0,66
| 9,02
| 5,04
| 17,58
| 17,96
| 0,67
| 9,39
| 5,27
| 18,44
| 18,83
| 0,68
| 9,77
| 5,52
| 19,37
| 19,77
| 0,69
| 10,18
| 5,79
| 20,36
| 20,79
| 0,70
| 10,60
| 6,08
| 21,43
| 21,90
| Примечание. для ; для .
|
ПРИЛОЖЕНИЕ 7 (рекомендуемое). МОСТОВАЯ СХЕМА НА ПОСТОЯННОМ ТОКЕ ДЛЯ НЕПРЕРЫВНОГО ИЗМЕРЕНИЯ И ЗАПИСИ ЭЛЕКТРИЧЕСКОГО СОПРОТИВЛЕНИЯ ЦЕНТРАЛЬНОЙ ЧАСТИ ОБРАЗЦА С ТРЕЩИНОЙ ПРИЛОЖЕНИЕ 7 Рекомендуемое
Образец нагружается растягивающей силой или изгибающим моментом .
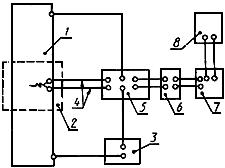
1 - образец; 2 - электрохимическая ячейка; 3 - стабилизированный источник тока (П 138); 4 - вводы; 5 - двойной мост (Р 329); 6 - микровольтмикроамперметр (Ф 116/1);7 - потенциометр; 8 - электронный потенциометр (КСП-4)
Образец укреплен в электроизолированных от корпуса нагружающего устройства захватах и уплотнен во второпластовой ячейке с коррозионной средой, в которой исследуется рост трещины. Через образец от стабилизированного источника проходит постоянный ток плотностью 0,01-0,1 А/мм . Падение напряжения на центральной части образца с помощью вводов подается на двойной мост. Вводы приварены к образцу точечной сваркой или зачеканены. Точки присоединения вводов к образцу рекомендуется располагать в начале механического надреза и фиксировать расположение этих точек по отношению к надрезу с погрешностью 0,1 мм. Вводы защищены от воздействия коррозионной среды химически стойким лаком или эпоксидной смолой. Нулевым прибором двойного моста служит микровольтмикроамперметр, выходной сигнал которого через согласующий потенциометр подается на электронный потенциометр.
До начала нагружения двойным мостом измеряют электрическое сопротивление образца; после нагружения и начала роста трещины электрическое сопротивление образца увеличивается, что приводит к разбалансу моста, величина которого записывается электронным потенциометром. При достижении конца шкалы потенциометра проводят повторную компенсацию и т.д., снижая чувствительность многопредельного микровольтмикроамперметра по мере увеличения скорости роста трещины.
С помощью схемы можно измерять приращение трещины менее 0,001 мм (после прогрева приборов в течение 3 ч и термической стабилизации не ниже 0,5 К). Ни один из приборов схемы не является обязательным и может быть заменен другим прибором, имеющим те же показатели чувствительности и класс точности.
ПРИЛОЖЕНИЕ 8 (рекомендуемое). СХЕМА ПРИСПОСОБЛЕНИЯ ДЛЯ ОПРЕДЕЛЕНИЯ KIKP ПРИ ПОСТОЯННОЙ ДЕФОРМАЦИИ НА ТОНКОЛИСТОВЫХ ОБРАЗЦАХ ТИПА ВРIПРИЛОЖЕНИЕ 8 Рекомендуемое 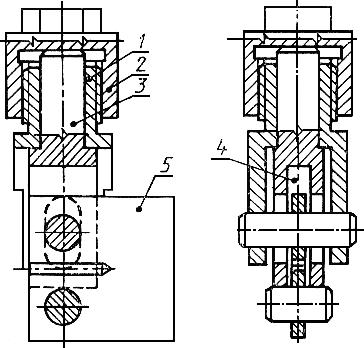
1 - винт; 2 - гайка; 3 - шток; 4 - продольный паз; 5 - образец
Образец нагружают двумя штырями с помощью винтовой пары и штока, имеющих продольный паз для размещения образца. Винт через отверстие связан с верхним штырем, а шток своим торцом контактирует с нижним штырем. Гайка глухим торцом перемещает шток в полости винта, осуществляя тем самым взаимное смещение нагружающих штырей и деформирование образца.
|